铍冶金方法及主要技术特点
金属铍冶金制备过程流程长,首先是将铍矿石按照特定的工艺方法制备成氢氯化铍,随后以氢氧化铍为原料制备具有一定纯度的氟铍化铵晶体,将氟铍化铵加热分解成玻璃状的氟化铍;用镁将氟化铍还原成金属铍珠,将金属铍珠经过真空感应熔炼去除金属镁、镁盐等杂质,即可制备出金属铍铸锭。铍冶金方法主要是指氢氧化铍的不同制备方法。铍冶炼的原则流程:铍矿石——>氢氧化铍——>氟化铍——>铍珠——>铍锭——>铍粉——>成型。
氢氧化铍的制备
从矿石中提取氢氧化铍的生产方法大体可分为氟化法、硫酸法、硫酸—萃取法和硫酸—水解法。
A 氟化法
将70%通过200目的绿柱石矿粉与硅氟酸钠(Na2SiF6)、碳酸钠混合,并制团。然后在隧道窑内于750℃下烧结2h,铍变成可溶于水的铍氟酸钠:

回收的铁氟酸钠返回配料。实际上配料过程中约60%的氟来自回收的铁氟酸钠,其余则需补加硅氟酸钠。
氟化法涉及的是碱性溶液,不存在腐蚀,设备问题容易解决,无特别的除杂质工序,过程简单;缺点是烧结条件控制要求严格,产品中硅含量高,特别是浸出液温度高时,硅显著增高;另外,烧结时氟溢出,加重了防护和环保难度。
美国的卡威奇·铍利可公司(Kawecki Berylco Inc.)和日本 NGK公司曾经用氟化法生产过工业氧化铍。国内曾有过氟化法的小试或半工业试验,目前有限川峨眉山市中山新材料科技有限公司使用该方法生产氧化铍,年产氧化铍400%国外只有印度采用氟化法生产氧化铍。
氟化法处理的矿物是高品位(BeO>10%)绿柱石矿,低品位矿中一般指令有较多的含钙矿物(石灰石、萤石等)。烧结时,矿物中的钙会生成不溶的镀膜酸钙(CaBeF4)而影响铍的浸出。氟化法同样也不适应高氟矿,因为高氟敏感中的氟主要以氟化钙形式存在。
B 硫酸法
硫酸法分为不加熔剂与加熔剂(碳酸钠或碳酸钙)两种方法。前者即美国布拉什威尔曼公司曾经使用的流程,后者即德国德古萨(Degussa)流程。有拉什·威尔曼公司硫酸法流程的原理是基于矿物晶形结构的改变,先将绿柱石膏成熔体,迅速水淬,然后将水淬块进行热处理。磨细后的物料经浓硫酸酸化后,铍(硫酸铍)的浸出率高达91%,浸出液含BeO36g/L,矿石中的铝变成硫酸铝,其他金属杂质也变成相应的硫酸盐,硅则进入渣中被除去。加氨水中和湿出液并降温至20℃以下,硫酸铵和硫酸铝生成溶解度小的铝铵矾晶体,75%的糖被除去。

硫酸酸化、浸出后的溶液含BeO12~15g/L,蒸发到一定的浓度后,加入硫酸铵、冷却,溶液中的铝以铝铵矾结晶被除去。
与布拉什威尔曼公司硫酸法不同的是,除铝后液用分步沉淀的方法,在pH=5,氧化中和除铁;再提高pH=7~8,铍生成Be(OH)沉淀。虽然其产品质量比布拉什威尔曼公司硫酸法差一些,但可以满足铍铜合金生产的原料要求。
德古萨法铍的浸出率比布拉什·威尔曼公司硫酸法高,但硫酸的用量是布拉什威尔曼公司硫酸法的1.6倍。
无论是布拉什威尔曼公司硫酸法或德古萨法,都以处理高品位绿柱石为基础。布拉什威尔曼公司进口绿柱石要求氧化铍含量大于11%;德古萨法在处理低品位铍矿时,虽然铍的转化率高,但渣量增大,浸出液含铍低。水口山六厂的经验证明:如果镀矿石品位低于9%,回收率将明显下降。对于高氟矿,则由于氧的存在,在铝铵矾结晶阶段除铝效率下降,较多的铝保留在溶液中,结果最终产品中铝超标。
C 硫酸—萃取法
1969年以前铍工业都以绿柱石为原料。绿柱石是一种铍铝硅酸盐,含 BeO 10%~12%。它的存在无规则,不易探测,无大型矿床。通常在伟晶岩中出现,作为开采长石、锂辉石、钽铌矿,锡石、钨矿的副产,用手选回收。依赖这种敏资源,可能影响到国防工业的需求,因此美国在20世纪60年代曾对国内各种矿床进行过评价。1969年,美国布拉什威尔曼公司决定在犹他州开采羟硅镀石。这是一种可用酸浸出的水合羟硅铍石矿,含BeO 1%,储量大,可以露天开采。从此,布拉什威尔曼公司摆脱了对绿柱石资源的依赖。
自犹他州铍资源显露商业开采价值时起,布拉什威尔曼公司就开始了羟硅镀石提取工艺的研究,1969年9月,用硫酸—萃取法从羟硅铍石矿中提取氢氧化铍的工厂投产。含BeO1%的矿石用稀硫酸浸出,得到含BeO1~2g/L、Al,0,7.5~13g/L的浸出液。浸出液用“D2EHPA-煤油”萃取,铍进入有机相(Fe、部分Al 也随同进入):
Be2+(水)+2(HA)2(有)=BeH2A4(有)+2H+(水)
有机相用(NH4)2CO3反萃,Be 以(NH4)2Be(CO3)2进入水相(Fe、Al亦随同进入)。将反萃液加热到70℃,Fe和Al变成氢氧化物或碱式碳酸盐沉淀被分离,进一步加热到95℃,铍以碳酸铍或碱式碳酸铵(2BeCO3.Be(OH)2)沉淀。在压力容器内打浆,加热到165℃水解产出碱式碳酸铵沉淀和含铍滤液,含铍滤液再加NaOH沉淀得到Be(OH)2。原则工艺流程如图10-4所示。
硫酸——萃取法使铍工业由依赖高品位绿柱石转向可大量开采的低品位矿石,意义重大。
D 硫酸—水解法
哈萨克斯坦乌尔巴冶金厂的铍生产流程原属于硫酸法,同样也因为原料的改变而发生了很大的变化。乌尔巴冶金厂的铍矿石原料来自俄罗斯赤塔地区的五一镇,矿物成分为硅铍石(4BeO . 2SiO2 . 4H2O)和似晶石(Be2SiO4),不能直接酸溶。原矿含BeO 1.2%,经选矿后达8%~9%。精矿的成分为:Be08%、AlO 8.7%、Fe,O11.7%、F6.7%、Mn1.1%。乌尔巴冶金厂处理这种矿石的工艺流程如下:
将矿石加5%的碳酸钠在1350℃下熔化,水淬,细磨,矿石中的铍转变成酸可溶皱;然后用硫酸酸化、水浸;铍、铁、铝都转变成相应的硫酸盐进入浸出液,大部分氟以HF或其他可溶氟化物同时进入浸出液;将浸出液加氨水中和,使铍、铁、铝分别生成Be(OH)2、Fe(OH)2、Fe(OH)3、Al(OH)3混合沉淀物;

将上述溶液煮沸,铍酸钠水解成Be(OH),铝保留在溶液中,从而实现了铍和铝的分离。据俄罗斯专家称,此方法的回收率达到95%。
水口山六厂根据俄罗斯专家提供的资料进行了探索,在试验室内走完了上述流程,回收率85%左右。主要问题是:碱消耗量大,每吨氧化铍增加成本6万元;废水量大,每吨氧化铍约1000t废水,其处理费用也会给成本带来压力。
矿石中提取氢氧化铍的生产方法对比见表10-7。
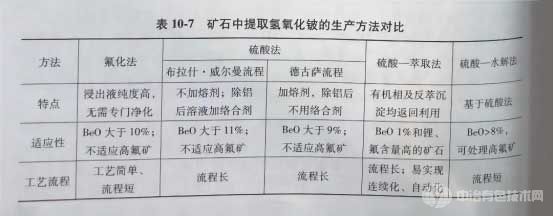

工业 Be(OH)2是生产工业氧化铍、高纯氧化铍、金属铍的原料。我国目前Be(OH)2冶炼工艺是由德古萨法改进而来,其工艺技术已基本成熟,但因铍矿资源的变化和硫酸工艺本身存在缺陷,导致生产存在诸多问题:工艺能耗高,金属回收率低(特别是随着矿石品位降低,回收率很难达到60%),Be(OH)2。产品质量不稳定,设备腐蚀严重,“三废”治理困难,劳动防护条件差,生产成本高等。