有色冶金烟气治理与资源化
低浓度SO烟气吸收法处理技术
火法炼铜厂低浓度SO2烟气包括炉窑(如干燥窑、阳极炉)烟气、制酸尾气和环集烟气等,这些废气中SO2。一般在400~5000mg/m³。《铜、镍、钴工业污染物排放标准(GB 25467—2010)》规定,这些废气 SO2≤400 mg/m³、硫酸雾≤40mg/m³才能达标排放。因此,低浓度SO2烟气治理技术在铜冶炼企业节能减排中具有重要作用。
低浓度SO2,烟气(3%以下)具有分布广、治理困难等特点。目前,在我国石灰石/石膏法脱硫技术应用最为广泛,但其副产物为利用价值不高的石膏,造成硫资源的浪费和二次污染。苛性碱法吸收速度快、效率高、无二次污染、低温催化转化,可降低成本且易工业实施。与国际先进水平比较,我国铜冶炼行业SO2减排还有一定潜力,目前我国各炼铜厂硫的总捕集率平均为99.0%,按年冶炼400 万t矿铜计算,将硫的总捕集率提升至国际先进水平的99.9%,则吨铜减排SO219kg,全国铜冶炼产业每年可减排SO27.6万t。SO2减排除采用“双闪”等先进的冶炼工艺外,最关键的措施就是加强环境集烟,采用高效的吸收技术,处理含低浓度SO2的炉、窑和环集烟气及制酸尾气。
低浓度SO2烟气治理主要采用吸收法,达数十种。我国铜冶炼行业应用的处理低浓度SO2烟(尾)气的方法有活性焦法、新型催化剂法、氨酸法、有机胺法(Cansolv)、亚硫酸镁清液法、苛性碱法等,这些方法各有利弊,在我国部分铜冶炼企业已有应用,技术成熟,应进一步推广。
(1)活性焦法
1)工艺流程
制酸尾气活性焦脱硫原则工艺流程如图6-10所示。该工艺催化吸附脱硫材料为圆柱体状活性焦。二吸塔出来的低浓度SO气体与水蒸气混合,于60~70℃下进入脱硫塔,在活性焦的催化作用下,生成硫酸吸附于活性焦微孔中。脱硫后的尾气达标排放。
2SO2+O2+2H2O——2H2SO4 (6-23)
吸附了硫酸的活性焦进入再生塔中,加热至400~500℃时,积蓄于其中的硫酸或硫酸盐分解脱附,活性焦得到再生。
2HSO2+C4——2SO2+2H2O (6-24)
再生的活性焦进入脱硫塔循环使用,含高浓度SO的再生烟气由风机送入制酸净化系统进行回收。
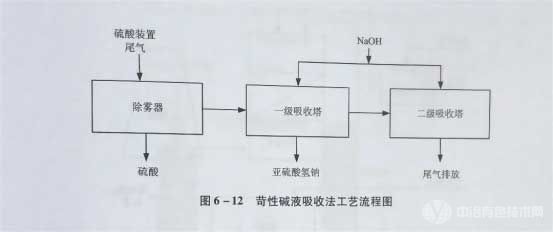
某大型炼铜厂制酸一系列活性焦脱硫系统脱硫塔入口及出口烟气量与成分、脱硫系统主要原料及公用工程消耗、所用活性焦规格性能等(设计值),分别列于表6-28~表6-31。
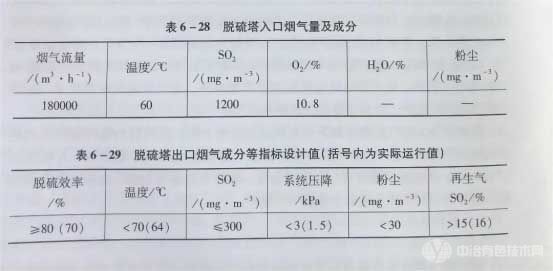
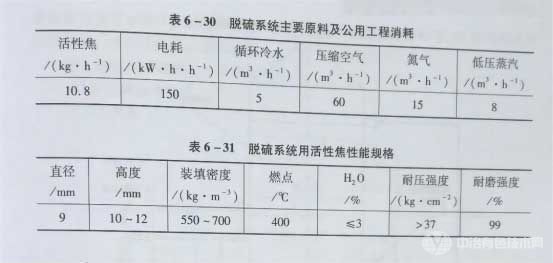
2)主要技术特点
脱硫效率较高,能满足现行环保标准要求;脱硫过程产品为高浓度SO,便于利用,无二次污染物产生;脱硫尾气温度较高,无需进一步加热;技术较为成熟,适应大型化;一次投资及运行成本偏高,脱硫装置占地较大。
活性焦脱硫法在江西铜业公司贵溪冶炼厂得到应用。
(2)氨-酸法
1)工艺流程
硫酸尾气氨-酸法两级吸收工艺流程如图6-11所示。来自硫酸装置二吸塔出口含SO2,及少量SO3、温度为60~80℃的尾气,进入第一尾气吸收塔,被亚硫酸铵和亚硫酸氢铵溶液吸收:
SO2+(NH4)2SO3+H2O=2NH4HSO3 (6-25)
SO2+2(NH4)2SO3+H2O=2NH4HSO3 +(NH4)2SO3 (6-26)
吸收反应使溶液中硫酸氢铵浓度不断增高,溶液对SO吸收能力降低,为此,不断向循环液中加入氨气或氨水:
NH4HSO3+NH3=(NH4)2SO3
第一级吸收后,尾气进入第二级吸收,两级吸收反应一致,但条件控制略有区别。设备紧凑。
如图6-11所示,两级吸收在结构上可设计为一个塔,分为上下两层,以使从第一级吸收塔循环泵出口设副线引出部分亚硫酸铵-亚硫酸氢铵母液,在混合槽中加浓硫酸将其转化为硫酸铵:
NH4HSO3+H2SO4——(NH4)2SO4+H2O+SO3
2NH4HSO3+H2SO4——(NH4)2SO4+2H2O+2SO2
为使亚硫酸盐转化完全,需加入过量硫酸,在中和槽中用氨气或氨水中和:
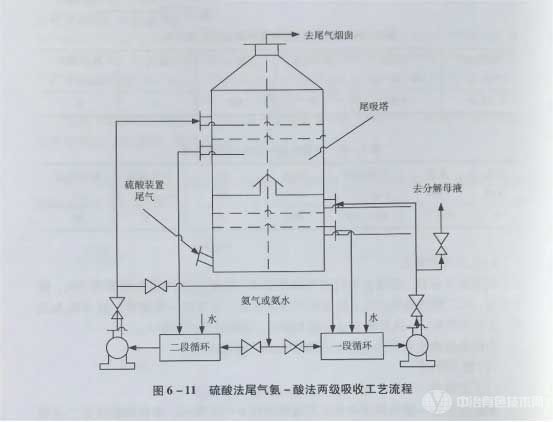
H2SO4+2NH3=(NH4)2SO4 (6-30)
混合槽放出含水蒸气的纯SO2,分解液中含有已分解释放而又溶解于分解液中的SO2,在分解塔中利用负压抽入空气脱吸SO2,分解塔出口SO2浓度5%,与混合槽SO2气体混合后送制酸系统,也可单独处理生产液体SO2。
母液分解得到的硫酸铵溶液,质量浓度400g/L,可直接或结晶成固态作为农肥销售。
第一尾气吸收塔亚硫酸盐质量浓度360~380g/L,S/C=0.8(S/C指溶液酸度,即吸收液中亚硫酸氢铵与亚硫酸铵的比例),密度1.18g/cm³。
第二吸收塔进一步吸收SO2,使尾气中SO2浓度达到100mg/m³左右。其吸收液S/C=0.82,亚硫酸盐浓度比第1吸收塔稍低。
2)技术特点
氨-酸法技术成熟,操作简单,设备维修方便,装置占地面积小,工程投资如按300万t/a制酸规模估算约需750万元。系统阻力小,脱硫效率高,能确保达标排放。原料氨来源方便,产品硫酸铵可作为农肥利用。
氨-酸法的主要缺点是若操作不当,易造成烟囱冒白烟,因此,要做到系统密封,严格执行操作规程,硫酸装置生产操作稳定,转化、吸收率比较高。氨-酸法尾气含有水蒸气,烟囱材质宜采用铝材或硬聚氯乙烯塑料等,外用钢材或玻璃钢加强,也可以采用玻璃钢烟囱。
氨-酸法在云南铜业公司得到应用。
(3)苛性碱液吸收法
1)工艺流程
苛性碱液吸收法工艺流程图如图6-12所示。来自制酸二吸塔的尾气,经过一级和二级吸收塔与NaOH溶液逆向接触,发生吸收反应:
SO2+2NaOH=Na2SO3+H2O (6-31)
Na2SO3+SO2+HO2=2Na2HSO3 (6-32)
第一级吸收塔在酸性条件下吸收,确保生成亚硫酸氢钠,第二级吸收塔在碱性条件下吸收,确保尾气达标排放。
质量分数为20%的NaOH溶液由二级吸收塔加入,控制循环液pH约为9.5,确保尾气达标排放;当一级循环液pH降为4.5~5.0时,排出亚硫酸氢钠溶液,并由二级吸收塔循环槽引入部分循环液进入一级吸收塔循环槽。由于亚硫酸氢钠易于氧化为硫酸钠,因此在储存运输中应充氮气保护。
2)技术特点
苛性碱液吸收法技术特点为:脱硫效率高,达95%以上,装置运行可靠;脱硫剂20%NaOH溶液来源有保障;脱硫产品亚硫酸氢钠可作为产品就近销售;主要缺点是脱硫剂苛性碱价格较高及运行成本较高。
该法在国外肯尼科特公司Garfield铜厂用于环集烟气脱硫,日本东予冶炼厂用于制酸尾气脱硫。在我国金川有色金属公司等多家企业也得到应用。
(3)新型催化法
1)工艺流程
图6-13为新型催化法工艺流程图。新型催化法采用炭材料为载体,负载非钒低温活性催化成分,利用烟气中的水分、氧气、SO和热量,将SO转化为一定浓度的硫酸。制酸尾气经过增湿管段添加蒸汽,使其湿度和温度满足SO催化转化要求,然后进入装有催化剂的固定床中,发生硫酸生成反应:
SO2+1/2O2+H2O=H2SO4 (6-33)
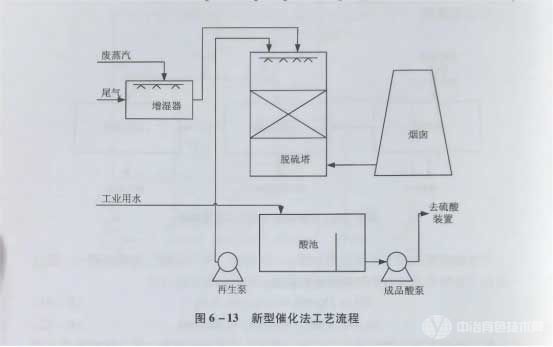
生成的硫酸吸附在催化剂载体微孔中,脱硫后的尾气达标排放。当催化剂内硫酸达到饱和后进行再生。再生采用梯级循环方式,采用不同浓度的稀酸进行分级淋洗,将床层内的硫酸转移到再生液中,催化剂活性得以恢复。催化剂静置沥干一段时间后即可再次使用。催化剂再生获得的较高浓度稀酸(20%~30%)经膜过滤后,返回硫酸系统作为补充水利用。
2)技术特点
工艺流程短,设备少,整个反应可在一个塔内完成,操作简单;适应范围广,温度在50~200℃,SO<3%的尾气均可适用;脱硫率高,净化后尾气SO<200 mg/m³,可满足严格的环保要求;脱除的硫以稀酸作为补充水进入硫酸生产系统,增加硫酸产量,有一定的经济效益;脱硫过程无“三废”产生,不会造成新的污染。
该法在大冶有色金属公司得到工业应用。
(5)有机胺法(Cansolv工艺)
1)工艺流程
有机胺法工艺流程如图6-14所示。若烟气含有粉尘和SO2,则需对其进行洗净预处理。低浓度SO烟气进入到吸收塔中,与贫胺溶液逆向接触SO2被吸收。
该法所用有机胺为一种二元胺,有2个氨基,一个为强碱性,一旦其与SO2 或强酸发生反应,则不可通过加热再生,而在脱硫过程中保持为胺盐形式,使得有机胺不会挥发或氧化分解:
NR1R2R3NR4R5+HX=H+NR1R2NR3R4R5N+X- (6-34)
第2个氨基碱性较第1个弱,称之为“吸收氮”,在脱硫中促进SO的吸收:
SO2+H2O=H++HSO3- (6-35)
H+NR1R2NR3R4R5N+H+=H+NR1R2NR3R4R5NH+ (6-36)
吸收了SO2的富胺液,进入再生塔中,与低压蒸汽逆流接触,在蒸汽的加热和携带作用下,脱除SO2:
H+NR1R2NR3R4R5NH++HSO3-=H+NR1R2NR3R4R5N+SO2+H2O (6-37)
脱吸得到的含饱和水蒸气的纯SO2气体,可进入制酸系统生产硫酸,也可转化为液体SO2等产品。
SO2烟气中一般含有SO2等,吸收过程中会生成不能脱吸的硫酸等强酸,因此要定期抽出部分贫胺液,采用电渗析法净化脱除。
2)技术特点:脱吸的SO2,纯度高,可多方案回收利用;脱硫效率高,可达99%以上,可满足严格的环保标准;在弱酸性环境下运行,溶液腐蚀性小,系统不易堵塞,装置可长周期稳定运行;装置规模灵活,大小均可;吸收液有机胺挥发性低,热稳定性高,可长期使用,消耗较低。
有机胺法已在冶炼炉窑及制酸尾气脱硫中得到广泛应用。我国祥光铜业公司采用这一技术脱除阳极炉尾气中SO,脱吸的SO进入制酸系统制酸,提高了硫的利用率。
(6)亚硫酸镁清液法
1)工艺流程
亚硫酸镁清液法工艺流程如图6-15所示。该工艺采用亚硫酸镁和亚硫酸钠混合溶液,在吸收塔中与烟气逆流接触吸收SO2:
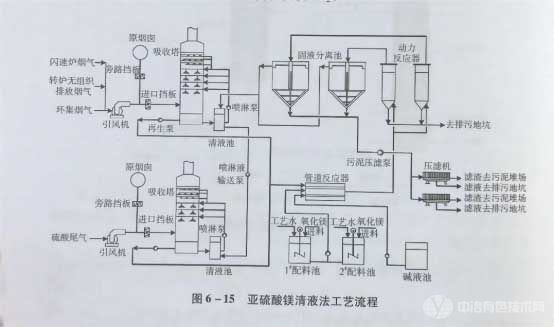
MgSO3+SO2+H2O=Mg(HSO3)2
NgSO3+SO2+H2O=2NaHSO3
溶液再生反应为:
MgO+Mg(HSO3)2=2MgSO3+H2O
MgO+2NaHSO3=MgSO3+Na2SO3+H2O
再生系统由再生泵、管道反应器、动力反应器和液固分离槽组成。来自配料系统的质量分数30%的苛性碱液和氧化镁浆液,在管道反应器中与吸附后液反应,生成高溶解性的亚硫酸镁和亚硫酸钠,然后在动力反应器中继续反应,氧化镁中的大颗粒杂质及反应结晶出的亚硫酸镁晶体,从动力反应器底部分离出来,进入固液分离槽。再生溶液返回吸收,分离出的亚硫酸镁污泥,在外排水氧化系统中将其氧化为硫酸镁,同时起到净水作用。
2)技术特点
脱硫率较高,脱硫剂为高浓度、高吸收活性的亚硫酸镁溶液,其脱硫效率高于95%,能将烟气SO浓度降低至50mg/m³;投资较低,采用高pH的清液循环体系,无腐蚀性,设备材质为普通碳钢,因此投资较普通的氧化镁法低10%以上;运行成本低,由于吸收液活性好,气液比为1500~2000,较其他湿法脱硫技术高,吸收液循环量小,脱硫塔阻力小,电耗低;运行可靠性高,烟气量波动适应性强;脱硫产物易于处理,但不能利用。
亚硫酸镁清液法在金隆铜业公司得到工业应用。
(7)我国铜冶炼厂应用较广的几种脱硫技术比较
国内某公司SO2无组织排放环集烟气量为1×10m³/h;烟气SO2浓度波动在1500~2000mg/m³,最高10000mg/m³;烟气含有一定烟尘。以此条件为依据,对国内炼铜厂常用的几种脱硫技术方案进行了比较,结果如表6-32所示。
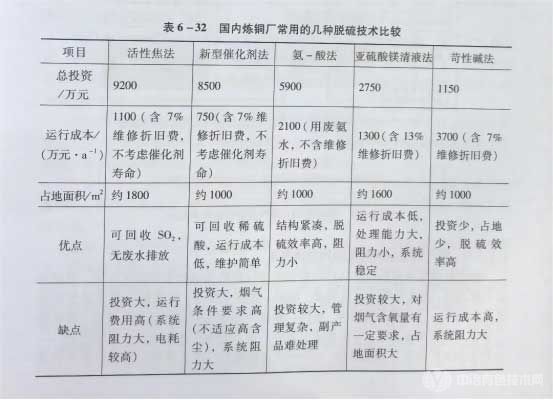